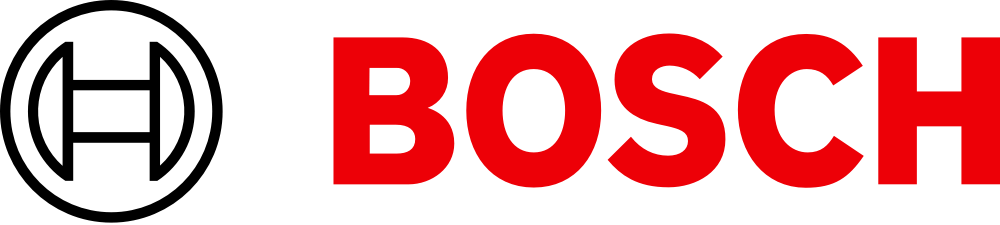
How they use elements
Driving global change with Boost (BOsch One Salesforce Transformation)
Bosch is multinational engineering and technology company known for its automotive parts, refrigerators, and power tools with close to $100 billion in revenue. It has embarked on a significant shift from a product-centric to a software-centric enterprise. The Mobility division which is over 60% of the revenue, embarked on a major transformation project called boost.Mobility. Boost stands for BOsch One Salesforce Transformation. The project impacts the 12,000 Salesforce users, across 8 divisions and 6 process streams.
The Bosch Salesforce implementation is complex, even though it is only 4 years old. It already has over 20 million records, 500 custom objects, and 6,000 Apex Classes. And this is not counting Managed Packages.
The Boost project is driving changes to support the new software and a content-driven business model. The current implementation was designed for a model where hardware was the product. The transformation was an opportunity to streamline and improve the implementation approach and ROI.
Reducing cost and increasing time to value
The underlying driver was streamlining their complex end to end process, but there were challenges due to the complexity and scale of the business operation and technology landscape:
Cost: High cost of implementation due to complex processes, that need to fluctuate. This was further complicated by disconnected or missing documentation.
Risk: Frequently broke the system while developing new features because of incomplete documentation of the configuration and difficulty in assessing risks.
Size: Large complex system with high levels of configuration, technical debt, and large volumes of data.
Speed: Long development cycles resulting in low customer satisfaction, with some features taking months to get into production.
Efficiency: Poor efficiency in designing and implementing new processes and features based on a lack of business analysis rigor.
4 core principles: Reengineering and retooling implementations
Underpinning the Boost project were 4 key principles and to deliver them required a robust platform for analysis and documentation. This is why Bosch selected Elements.cloud.
1
Idea 2 Release Process
A flexible and reliable implementation process to manage changes according to new requirements. It is a strict approach that needs to be followed to ensure that there are no shortcuts which lead to mistakes.
2
Ownership
Applied ownership to all areas: business processes and all metadata. For example: diagrams, objects, managed packages, flows. Whilst this required effort it solved one of the biggest pain points which was ensuring continuity when employees moved.
3
Data
Metadata and documentation used to assess risks as early as possible. This is made possible by a rigorous implementation process that relies on complete documentation.
4
Documentation
Streamlined and complete documentation connected to the source metadata and to the purpose for the change. With the large diverse implementation team, standardization, naming convention, and a common repository, Elements.cloud was critical.
Change Intelligence Boost
The Elements.cloud Change Intelligence Platform proved to be an invaluable tool across the Boost project. It supported a shared, centralized view of all the documentation standards and formats. This was across all stages of the implementation process, from Idea to Release. Using UPN process diagrams improved shared ownership and understanding of the business processes and the required changes to Salesforce. The integration with Jira enabled synchronized requirement management so the development teams were coordinated with the business. The integration with Salesforce accelerated onboarding of new team members, thereby reducing training time and improving productivity. The ability to assess the impact of any dependent metadata changes, reduced risk and accelerated the speed in which changes could be delivered.
Strategic Goals
The top-down process diagrams and capabilities modes linked to the metadata reference model are a strategic move to align business objectives with IT capabilities. By connecting company KPIs with process and data models, Bosch aims to create a more cohesive and efficient operational framework. This alignment is expected to drive better performance and supports Bosch’s long-term strategic goals.
Looking ahead, Bosch is considering migrating to Salesforce’s Manufacturing Cloud. The robust documentation will enable better assessment of the changes that will need to be made and the overall implementation risk and effort.
Talk to us
Connect with the Elements team today to discover the breadth of capabilities that our Change Intelligence Platform has to offer.
How they use elements
Unleash Your Potential
Build your Centre of Excellence with Elements.cloud